Why Inverted Flare Fittings Are Essential in Hydraulic Systems
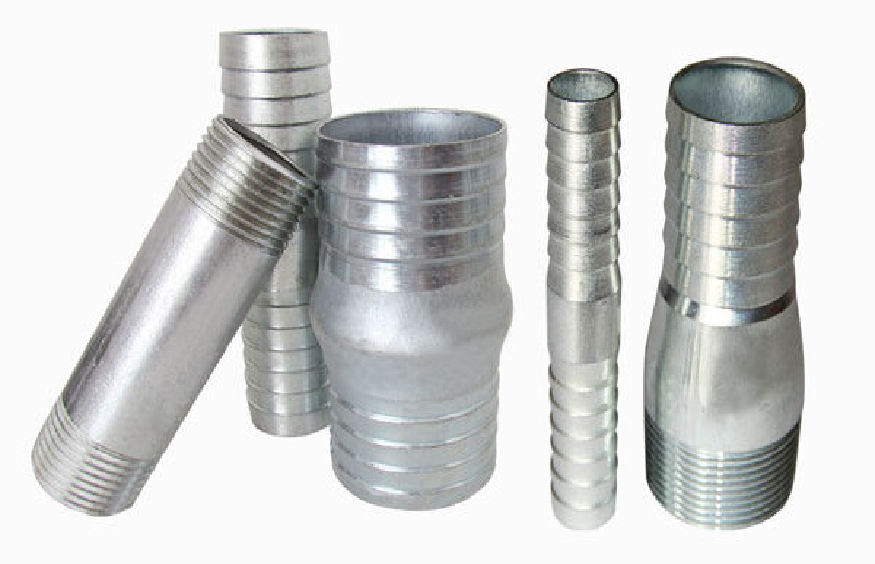
Hydraulic systems are intricate networks that rely on a multitude of components working seamlessly together. Among these components, fittings play a crucial role in ensuring fluid flow, system safety, and reliability. One type of fitting that stands out in importance is the inverted flare fitting. This blog explores why inverted flare fittings are indispensable in hydraulic systems and how they interact with other elements such as copper nickel fuel lines and brake line tubing.
The Role of Inverted Flare Fittings
Inverted flare fittings are designed to create a tight seal in hydraulic systems by using a unique design that involves a 45-degree flare on the end of the tubing. This design ensures a secure connection, which is essential for maintaining pressure and preventing leaks. The inverted flare fitting is particularly favored for its ability to provide a leak-proof seal even under high-pressure conditions.
This type of fitting is commonly used in various applications, including automotive and industrial hydraulic systems. Its reliability stems from the way it seals: the fitting’s flare contacts a matching seat, forming a tight, reliable connection that withstands vibrations and pressure changes.
Compatibility with Copper Nickel Fuel Lines
A copper nickel fuel line is a popular choice in hydraulic systems due to its excellent corrosion resistance and durability. These lines are often used in applications where longevity and resistance to harsh environments are critical. Inverted flare fittings complement copper nickel fuel lines perfectly, as they are designed to accommodate the properties of these materials.
The 45-degree flare on inverted flare fittings matches well with the ends of copper nickel fuel lines, ensuring a secure and leak-proof connection. This compatibility helps maintain the integrity of the hydraulic system and extends the lifespan of the components involved.
Integrating 3/16 Brake Line and Brake Line Clips
Inverted flare fittings are also integral to brake line systems, particularly when working with a 3/16 brake line. The 3/16-inch brake line is a standard size used in many vehicles, and inverted flare fittings provide a reliable connection point for these lines. The design of the inverted flare fitting ensures that the brake line remains securely attached, which is crucial for safe braking performance.
Brake line clips are another important component used in conjunction with brake lines and inverted flare fittings. These clips help secure the brake lines in place, preventing movement and potential damage. By combining inverted flare fittings with brake line clips, the brake line system remains stable and functional, reducing the risk of failure and enhancing overall safety.
Advantages of Copper Nickel Brake Line and Brake Line Tubing
A copper nickel brake line offers several advantages over traditional steel brake lines. They are more resistant to corrosion and have a longer lifespan, which is beneficial in maintaining a reliable hydraulic system. When paired with inverted flare fittings, copper nickel brake lines form a robust and durable system that can withstand various environmental conditions.
Brake line tubing, which comes in various materials and sizes, also benefits from the use of inverted flare fittings. The fittings ensure that the tubing remains securely connected and leak-free, regardless of the material used. This versatility makes inverted flare fittings a valuable component in a wide range of hydraulic and braking applications.
Conclusion
Inverted flare fittings are a crucial component in hydraulic systems, offering reliability and leak-proof performance. Their design makes them compatible with various materials, including copper nickel fuel lines and 3/16 brake lines. By ensuring a secure connection, these fittings play a significant role in maintaining the safety and efficiency of hydraulic and braking systems. Whether you’re working with copper nickel brake lines or integrating brake line clips, inverted flare fittings prove to be an essential part of a well-functioning hydraulic system.